

This robotic submarine project, required six laser enclosures capable of withstanding up to 3000 PSI of water pressure, on dives of up to one mile deep under the Antarctic ice sheet.
​
The housings were designed in Fusion360 and 3D printed by PolyImpact. The polycarbonate end caps were cut on the in-house CNC router from the same Fusion360 file.
​
The forward bulkhead was also modified on the CNC router to accept the forward laser housing.
​
The prototype was pressure tested in the client's test tank. It withstood an initial 3000 psi, then 2000 psi for 24 hours, which met the test criteria.
​
The lasers were installed on the ROV and successfully deployed in Antartica.
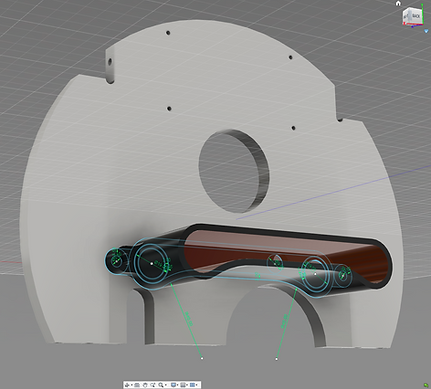
3D Rendering and Graphic Design
by PolyImpact
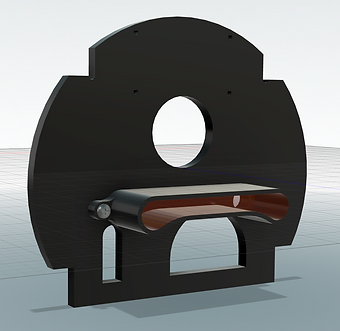

Forward laser housing mounted on forward bulkhead.

Forward laser housing filled with oil based potting material which is waterproof and which distributes ambient pressure evenly across all components.
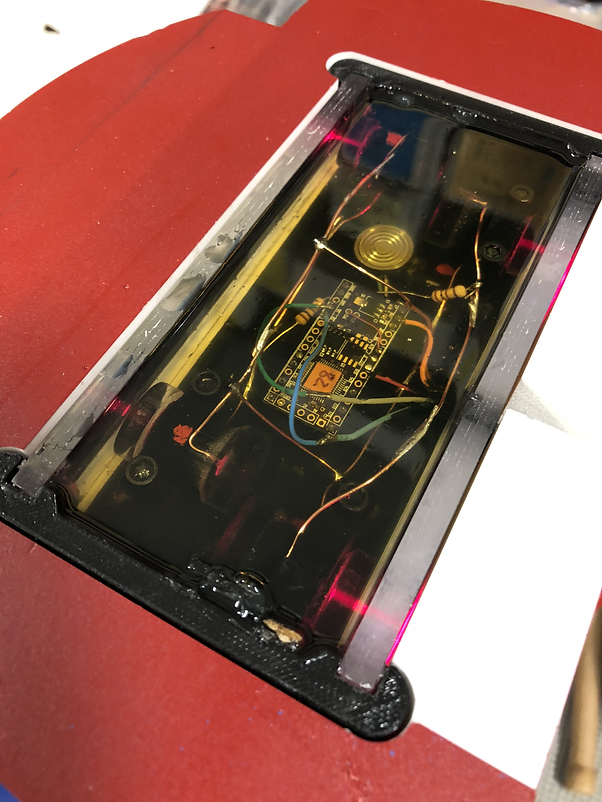
At left is the Midship Laser Bay.
The four lasers are firing through potting material and polycarbonate lenses.
​
In addition to the four laser enclosures shown here, the black plastic large enclosure, and the two polycarbonate windows were also produced by PolyImpact.
Purpose:
There are three cameras aboard the SCINI ROV.
One looking forward, one straight up amidship and one straight down amidship.
​
There is a pair of lasers for each camera. The lasers are exactly 10 cm apart and their beams are parallel.
As a pair of beams strikes an object, this known 10 cm spacing is used to determine the size of the object in the camera image.
​
(Laser alignment shown below.)
